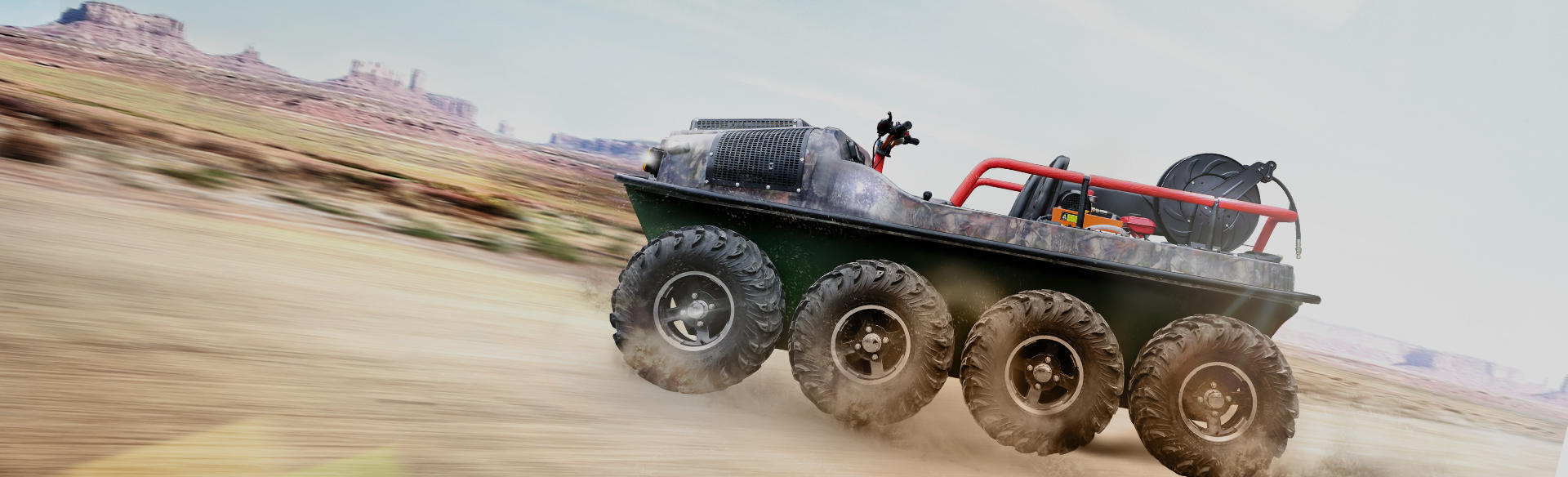
How to repair gravity casting crack defects
If the strength of the alloy exceeds this temperature, cold cracking, or cold cracking, occurs. The cold cracks formed at low temperature have small defects, continuous and straight, clean in the seam, and occasional slight oxidation. Special-shaped parts, especially castings with large wall thickness differences, especially large thin castings, are prone to cold cracks. Typically, a step to reduce internal stress in the casting or reduce the brittleness of the alloy is to protect the formation of cold cracks. For example, iron and phosphorus in iron will significantly reduce the impact resistance of the alloy, increase the brittleness, and easily lead to cold cracking, so strict restrictions should be placed on smelting metals.
Simple rough casting. Generally, the repaired parts do not need follow-up treatment, and there is no special hardness requirement. The added value of such castings is low. Welding repair materials: More than 90% of foundries choose welding repair materials to solve casting defects encountered in production. Due to the use of metal filler materials (the welding materials generally match the casting materials), the welding repair performance can basically reach the standard of the base metal, the operation is simple, and the welding repair efficiency is high, which has been recognized and trusted by many manufacturers.
Using the principle of instantaneous high-frequency discharge, stick the weldment on the surface of the workpiece, and the thickness of the sticker is consistent with the thickness of the weldment. Welding quality depends on whether the discharge is uniform. It is suitable for workpiece wear and repair of out-of-tolerance machining, which has a certain impact on the mold market. The machine can also fill defects such as blisters with solder powder (or machining waste) and repair them with electrical discharge. The chromatic aberration of the repaired workpiece is small. The disadvantage is that the patching speed is slow.